SemiConductor Heat Chamber Automation Saves Space & Cabling Costs
Motion occurs in all facets of manufacturing, and the semiconductor industry is no exception. The $370 billion semiconductor industry employs a workforce of one-quarter million direct jobs in the U.S. alone, and has been a key export of the United States over the past decade. While scanning silicon wafers for defects, motion control systems are used to move the vision inspection equipment steadily over the delicate wafers.
A SmartMotor™ connected to an actuator moves inspected wafers up through a vacuum sealed chamber for the metallization/ deposition processes. Automation is also essential in the dicing process for those same silicon substrates that are then separated into the individual microcircuits. Even the packaging of the final products often employs input/ output stacking and multi-axis pick and place applications. In the growing energy industry, several types of solar cells are made from similar silicon wafers and with the green/ solar industry heating up, efficiency and precision in all manufacturing automation of silicon wafer processes are essential for this emerging market's survival.
Automation Communication Problem Solved by Animatics
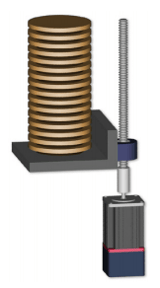
Animatics was recently approached by one of the largest suppliers of semiconductor manufacturing equipment to help solve their automation communication problem. After using a controller and motor system for an elevator that separated wafers into different slots to be taken into a heat chamber, the company could no longer find a motor in production that fit their 15+ year old controller. The motor they used drove a pulley to ball screw to align the wafer with the correct slot before a robotic arm took the wafer into the chamber. The problem was whatever new motion system they selected to replace the separate motor and controller system had to be able to understand command protocol from their host system. The alternative, changing the command protocol in their state of the art system just to accommodate the motor’s language, was not an option.
Why SmartMotor?
Choosing the SmartMotor™ solution, the user was able to create a parser in the SmartMotor program to parse ASCII character command strings from the host. The SmartMotor program then decoded the command strings to set motion parameters and initiate motion. In order to achieve this, the parser needed to run extremely fast in the user’s program, and the Class 5 SmartMotor had the processing power to execute it all.
“We were able to reprogram our SmartMotor to parse their command string. The interrupt feature in the Class 5 SmartMotor made it way
easier to control the structure of the program, especially the parser,” said Minh Tran, Sr. Application Engineer for Animatics. Because of this capability, Animatics was able to replace the entire controllermotor setup with a single integrated NEMA 34 frame SmartMotor and precisely simulate the old controller without changing the command protocol of the host. Though a few competitors could be programmed in a similar fashion, it was the execution speeds of the Class 5 processor that made SmartMotor the obvious choice, saving space and cabling costs for the heat chamber's automation system.