Dedicated SmartMotor™ Firmware Creates Custom Spooling Patterns to Eliminate Product Waste
Simple winding of material onto spools is a common practice, but precision winding that prevents material damage, which can be easily implemented, and provides a substantial and quick ROI is another story.
Material such as fine copper wire or fiber optics cannot be kinked or jammed between prior layers of wound material on the spool. This could damage the material and lead to drops in signal quality and reduced product life. The risk of material breakage or jamming reduces production line throughput for the end user as well.
To provide optimal winding of these materials, each layer must be wound in a way that prevents it from getting stuck in the previous layers. To do so requires a special pattern of winding each layer at an opposing angle to the previous layer so that the material never runs along a path parallel to the underlying layer. This method prevents the material from getting trapped or kinked when additional layers increase forces inward on the spool.
Traditional winding operations are similar to that of a fishing reel mechanism, which simply moves back and forth across the spool as it is rotated.
Simple mechanical spooling
This is a proven method for simple applications. It uses basic threaded gears or electronic gearing to perform the action. If the system is purely mechanical, then it will only work for a set size of spools and material thicknesses. This reduces flexibility and increases production floor space with the addition of dedicated machines for each product. Moving to electronic gearing adds flexibility within one machine for handling different product thicknesses. However, it still doesn’t address the primary issues of kinked and jammed product caused by the near-parallel paths of each layer.
SmartMotorTM servos have dedicated firmware just for traverse and take up profiles. But in addition, electronic camming may now be added on top of the traversing profile to enhance the traverse motion and provide a non-parallel layer to prevent kinking or jamming of the material. A typical setup is as shown here:
As shown above, the spool may turn several times during the traverse, based on spool width and material thickness. However, to get a pattern on top of that, which would prevent the kinking of material, the motion would have to deviate from a linear to nonlinear path for every single turn of the spool. The following figure shows a motion profile for traversing the length of the spool with an overlaying cam per every single revolution of the spool.
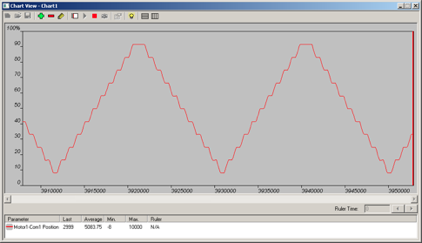
Traverse and cam motion profile
The motion of the traversing (slave) motor creates a step motion from one end of the spool to the other, where camming (high-frequency oscillation) occurs on top of gearing (low-frequency traverse). The SmartMotor allows this method to be implemented using only four parameters for traversing and a single cam table set to cycle for each revolution of the spool.
As shown in the following figure, the spooling pattern created by this method ensures the material does not fall between previously wound layers, which could cause the spooled material to tangle or break when later attempting to unwind the spool.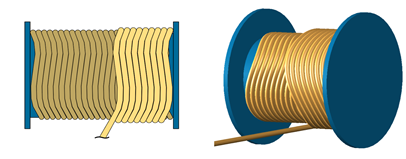
Spool created by camming summed in with traversing profile motion
Key Benefits:
Although high-end controllers that can overlay camming on top of gearing profiles are available, they are expensive to purchase and complex to integrate. Whereas, the SmartMotor integrated servo employs advanced gearing and camming to provide a robust solution that is simple, compact, and cost effective. With the SmartMotor, motion is controlled at the highest possible priority through firmware (no active program code running), which ensures highly accurate material positioning for spooling without material damage.
To illustrate, consider the following key cost savings when comparing a traditional spooling solution to the sophisticated SmartMotor solution:
Key Savings |
Traditional Spooling |
SmartMotor Solution |
Avg. Cost Per Axis | $4000 - $5500 | $2000 - $3000 |
Time-To-Market | 1-2 weeks | 3-5 days |
Setup Complexity |
High; lots of wires and components involved. Lengthy integration effort. $$$ |
Low; minimal cabling and an integrated, powerful controller. No PLC needed for complex winding patterns. $ |
Ease of Programming |
Low; lacks specialized firmware. | High; built-in firmware commands for quick and easy programming. |
Ease and Speed of Machine Replication | Low; requires separate drive and controller, and larger panel space. | High; fully integrated, compact, embedded firmware capability has done the heavy lifting. |
Versatility | Low; each product requires a dedicated machine or compromising on end result. | High; can be quickly modified for multiple products to meet exact specifications |
Work Throughput | Low; great risk of material tangling or breaking by falling into gaps of prior layers of material. | High; complex wind patterns significantly lower the risk of damage or breaking. |
In summary, the SmartMotor allows you to:
- Minimize programming time by easily changing a few motion parameters to fit various material widths and spool sizes
- Speed product changeover (rapid change-out or change over) by running a multitude of patterns with a single SmartMotor
- Minimize equipment and machine-build costs by replacing expensive motion controllers, cabinets, and wiring with just the SmartMotor integrated controller
- Reduce programming effort and time-to-market through the wide variety of predesigned spool patterns
- Machine designers can run virtual axis testing and plot all wind patterns in real time at their desktops before the control cabinet is even populated
Examples of Critical Winding Applications:
Industry |
Application |
Aerospace |
Aircraft fuselages (carbon fiber). |
General Industrial | Motor armatures. Air filter production: media for submicron-sized filter elements. Capacitor or transformer coils. Film-insulated magnet wire. Precision sensors and transducers. Filament winding (glass, carbon graphite, etc.) for pipes, pressure vessels, golf club shafts, power transmission and distribution poles, etc. |
Medical | Catheter production. Tubing. Dental floss. |
Metals | Copper wire. Precision-slit, stainless-steel coils. |
Semiconductor/Photonics | Fiber optic cable, inductor and choke coils manufacturing. |
Sound Engineering/Music | Edge wound voice coils. Guitar strings. Microphone coils. |
Telecommunications | Cable winding. |
Textile | Thread and yarn production. |
Contact Moog Animatics or your sales rep today to find out how the integrated SmartMotor servos and software can immediately solve your most challenging spooling applications.