SmartMotor Assists Plasma Cutter with Power and Precision
Metal is vital to modern industrial design because of its durability, solidity and strength, but these properties also make it extremely difficult to penetrate. The technique of plasma cutting has become a popular solution, though not an exceptionally accurate one. With plasma cutting, the strongest metals can be completely severed using an ionized, high powered stream of gas sent through a small nozzle, creating an arc. The electric arc heats the gas to such an extreme temperature that it becomes plasma, simultaneously melting the metal and clearing away the metal debris.
The Challenge
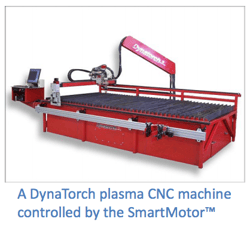
To cut such intricate designs out of metal such as the one above, DynaTorch™ Inc. needed to create an extremely accurate CNC plasma cutter, and they found no better servo than the Animatics SmartMotor™ to achieve the power and precision they needed.
How SmartMotor Helped
SmartMotor™ technologies utilize a true servo, unlike steppers that lead to unacceptable problems such as error accumulation and missing steps. The higher speeds achieved in plasma cutting with the SmartMotor™ technologies meant increased throughput and profits for DynaTorch™. With the SmartMotor™ servo’s internal controller and memory storage, DynaTorch™ was also able to create dynamic CNC software for their cutting systems featuring DXF and G-Code conversion.
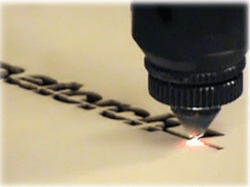
The software developed was such a success that it was included in the foundation for Animatics’ full-featured CNC software package: JenCNC™. Though new, JenCNC™ has already been used across multiple industries in machines such as routers, adhesive applications, and milling machines.
The most impressive feature of the DynaTorch™ system with the SmartMotor™ is its ability to precisely control the height from the nozzle of the plasma cutter to the metal’s surface. The onboard I/O of the SmartMotor™ was used to create a closed loop feedback based on the measured arc voltage. Considering that arc voltage is proportional to the distance between the nozzle and cutting surface, the plasma cutter was programmed to maintain an exact height over the metal despite frequent inconsistencies in the metal’s surface and thickness. Achieving simplicity, power and results with the SmartMotor™, DynaTorch™ is another very content Animatics’ customer.
Download the PDF version of this case study here.