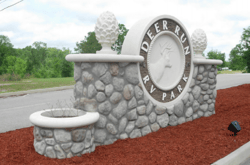
SmartMotor Assists Foam Sculpting Tool
Realistic 17th century Spanish cannon? Yes. Prototype for a new Lamborghini? Of course. Life-size rendition of Michelangelo’s “David”? Absolutely! All of this and more out of giant blocks of foam with the help of Animatics’ SmartMotor™ and JenCNC™… why not?
These are just a few of the many products that Blockwire Manufacturing in Goshen, Alabama has created for their customers. Blockwire specializes in EPS foam cutting: a popular method for designing and producing high quality expanded polystyrene (EPS) foam core monuments, 3D signs, sculptures and prototypes. In the first part of the process a thin, taut metal wire is heated with electrical resistance to approximately 200 degrees Celsius. This “hot” wire vaporizes the foam just before any contact is made and cuts the foam into manageably sized blocks. For the sculpting artistry that brings in the business, the foam blocks are transferred to a router with a spindle on a multi-axis CNC frame where all of the intricate details on the sculptures are carved.
How It Works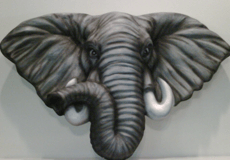
The router is used to transform bland blocks of foam into any shape imaginable, from ivy detail on roman columns to replica sculptures, jagged rock walls and beyond. Blockwire utilizes four SmartMotor servos on their router: 2 on the X-axis, 1 on the Y-axis and 1 on the unique 18-inch Z-axis.
Blockwire also took advantage of Animatics’ JenCNC program: software combining CAD/CAM and motion control capabilities into a unique graphical user interface, to coordinate all SmartMotor servos in 3D coordinated motion.
Why SmartMotors
Accuracy is integral to stay competitive in Blockwire’s specialized industry, and the accuracy of the foam cutting system is dependent on the precision of the motors used and the backlash of the drive systems. Originally Blockwire had chosen stepper motors to control the axes, but inaccuracy and failure was a constant problem. “I felt like my machine and I just couldn’t get along. Every time I turned my back, something would go wrong. It was very time consuming” said Jeff Ryan, founder of Blockwire.
Ryan decided to gut the system and start over with SmartMotor servos and JenCNC instead. Although this was a major change for the company, it was also a tremendous improvement.
“I can’t remember a single failure from the SmartMotor that wasn’t explainable by some programming error or outside cause. They’ve been very reliable, and that’s exactly what I needed. Since it’s an integrated servo, I didn’t have to learn all of the inner workings of the motor in order to get my machine working, and that saved a lot of time and headache.”
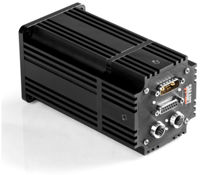
Ryan also took full advantage of Animatics’ dedicated technical support when designing his machine and the few phone calls with his “SmartMotor therapist” went above and beyond expectation.
What's Next
Now Blockwire is using SmartMotor and JenCNC to take their projects to the next level of complexity. Recently they were asked to produce a foam prototype of the engine casing for the nose of a new single engine, lightweight aircraft currently under development. The planes engineers plan to use the full-scale foam plug to create a fiberglass mold for parts and testing.
Download the PDF version of this case study here.