SmartMotor™ Used for Pharmaceutical Industry
A customer from a large pharmaceutical industry recently came to Moog Animatics with the need to rapidly transfer pill bottles on and off a fast moving factory line for inspection.
They had an existing machine in place that used a 3-position pneumatic cylinder. The bottles were pulled off the line to a 90-degree position for inspection, a 180-degree position for processing, and then returned to the line.
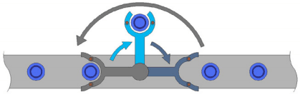
The Challenge
The speed of the line was severely limited by the inherent inability of the air cylinder to stop quickly and accurately enough in mid-stroke. Additionally, there were issues with flow control. Air cylinders have no ability to control the motion profile of a move or accelerate and decelerate at any predictable rate. This rapid and abrupt stop of the cylinder caused the bottle to become unacceptably misaligned in the grippers. When this happened, the line would sometimes be stopped to correct the misalignment, wasting valuable time and resources.
Reducing air pressure to the cylinder reduced the occurrence of misalignments; however, the sacrifice was significantly reduced line speed below acceptable throughput.
The engineers at this company sought out a servo driven system as their solution. SmartMotor™ integrated servos were able to use a 50:1 gearhead and fully controlled motion profiles to increase overall line speed while virtually eliminating misalignments.
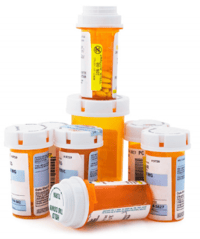
Normally, switching a significant piece of machinery has large costs from updating the systems that control that machinery. A significant cost saving feature that SmartMotor™ integrated servos have in this realm is the ability to be programmed to take existing I/O or serial commands from existing control systems.
Why SmartMotor™
This company was able to use the exact same commands that triggered the air cylinder, to control the SmartMotor™. There was no change to the
PLC code that controlled the system. Putting in the new motor and gearhead was essentially the only change. Because the SmartMotor™ has
fully integrated motion control electronics, power amplifier, encoder, and communications, all that was needed was a power supply and communications cables. This allowed reduced development time, increased throughput and reliability, and more straightforward
troubleshooting in the future.
Download the PDF version of this case study here.