SmartMotors Enables Synchronized, Fluid Movement for Vertical Loading
Moving one vertical load is simple; moving countless loads in a small space is not. Coordinating the movement of 1,008 individual loads over a 40 foot vertical distance to create synchronized, fluid movement seemed impossible. That was the challenge set before Animatics during the production of FTSI Automation’s spectacular kinetic sculpture at The World Expo in Shanghai, China.
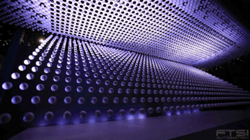
FTSI Automation’s project required a very large number of motors in very tight quarters to lift and lower their respective loads in such a synchronized, fluid fashion that the small, soccer ball sized spheres would appear to float and dance over a stage. They also required a Contouring Mode, so that one, a few, or all of the motors would be able to respond to impromptu commands in coordination. Installed cost was a large concern, and the ideal solution appeared to be an integrated drive, motor and controller package that would be compact enough for the tight setting, and Animatics quickly realized that the Class 5 SmartMotor™ would be an operable solution. The Class 5 SmartMotor™ system’s closed loop servo meant that positioning loss would not be a problem, and the integrated servo could maintain the high rates of speed that a stepper motor could not. An integrated brake was also included in each Class 5 SmartMotor™ to ensure that the whole structure would not come crashing down if there was a loss of power.
How SmartMotor Helped
The result was a breathtaking performance in Shanghai where 1,008 floating spheres snaked, waved and transformed into all shapes across the stage with such accuracy that it looked like a computer generated animation instead of a life-size production. Each of the 1,008 spheres attached to a wire had its own SmartMotor™ servo at the top, precisely creating and controlling every movement.
The Class 5 SmartMotor™ was able to provide continuous Contouring Mode at data packet rates fast enough to allow the fluid motion of all 1,008 motors, and it was programmable to home on demand to a hard stop without the need of an external home sensor. Its compact shape and design, integrated brake and up to 200 Watts of power at the shaft made it a strong competitor compared to other options, and its cost conscious pricing made it the clear choice.
Download the PDF version of this case study here.